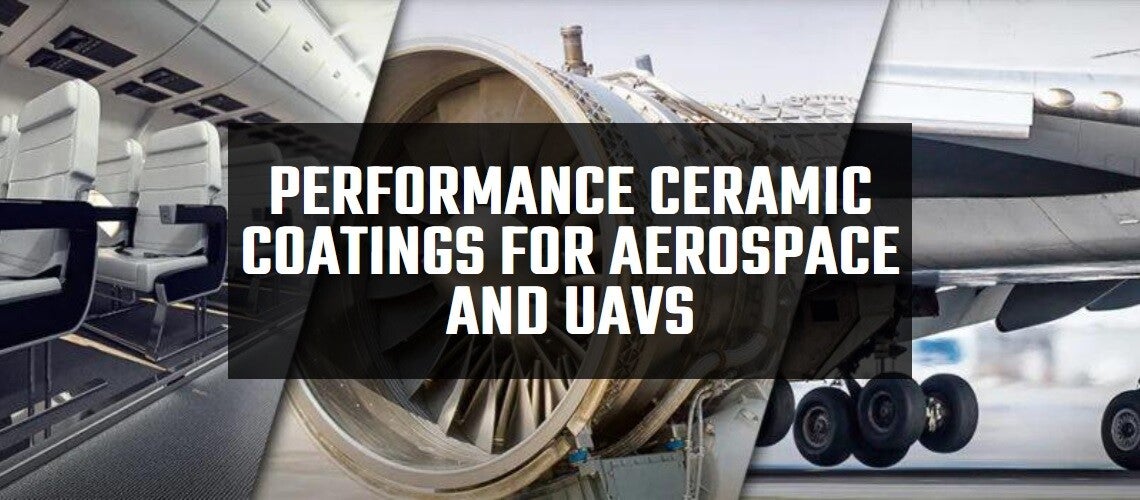
CERAKOTE IS USED IN THE AEROSPACE INDUSTRY ON EVERYTHING FROM INTERIORS TO EXTERIORS, ENGINES TO WINGS, ELECTRONICS, AEROSTRUCTURES AND MORE.
Cerakote is the global leader in the manufacturing of inorganic thin film ceramic polymer hybrid coating technology.
Cerakote:
- Can be applied to multiple substrates – Applies to ferrous and non-ferrous metals, alloys, polymers, composites and more.
- Is a single layer coating system – Replaces multi-layer paint and powder coating systems.
- Is a thin film ceramic coating that applies at only 0.25 – 2.0 mils, allowing for ultra-light weight coverage and protection.
- Has superior chemical resistance – Resistant to hydraulic fluids, fuels, solvents, acids, de-icing products, commercial strength disinfectants and more.
- UV stability – Protects substrates from oxidation and degradation.
- Is highly abrasion resistant – Withstands impact, scratch and gouging better than other coating systems.
- Offers high temperature coatings – Corrosion protection coatings that withstand up to 1,800˚F without spalling, cracking, or flaking.
- Has coatings that provide thermal barrier and heat dissipation.
- Offers alternatives for plating and pretreatments – Replaces anodizing, nickel plating, and the need for primers.
- Products are VOC exempt in all 50 states and are REACH/RoHS compliant.
- Has outstanding customer support including dedicated account managers.
FAA Testing:
Read on to learn more, or:
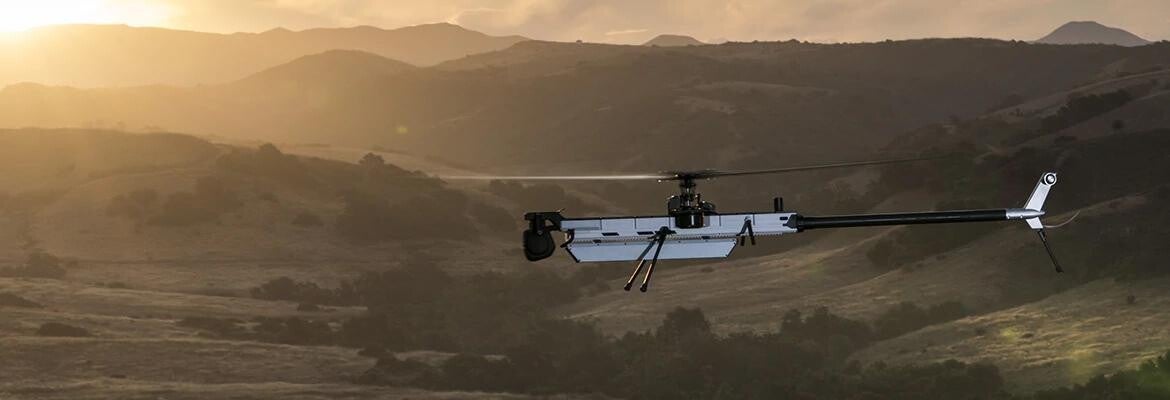
Image: “Anduril uses Cerakote on their drone systems for the protective properties (extreme corrosion and chemical resistance, unmatched durability) that our ultra-light weight ceramic based coatings are famous for.”
Cerakote is a performance coating known for its high-quality look, feel, and durability. Our inorganic formulations allow for maximum durability, excellent UV stability, extreme chemical resistance, and consistency across multiple substrates. We work with our customers around the world on customized solutions to solve industry problems and help them provide new marketable products.
In addition, our customers choose Cerakote for:
- Consistency of quality and product
- The ability to refurbish parts
- Large color variety
- Custom coating formulations
- Readily available and manufactured in the USA
Applications include:
- Aerostructures
- Cabin/Interiors
- Exteriors – latches, locks, window frames, leading edge components
- Flight deck surfaces
- Electronics
- Hardware/Fasteners
As the commercial space industry continues to grow, so have the requirements for new and better finishing technologies for the harsh environments of space. Cerakote’s unique inorganic ceramic coatings allow customers to protect their assets in space with commercial off-the-shelf options ready for integration. We offer coatings that:
- Pass ASTM E595-15
- Are resistant to atomic oxygen
- Are UV and high radiation stable
- Offer a low-reflective and light-absorbing finish in the visible light spectrum
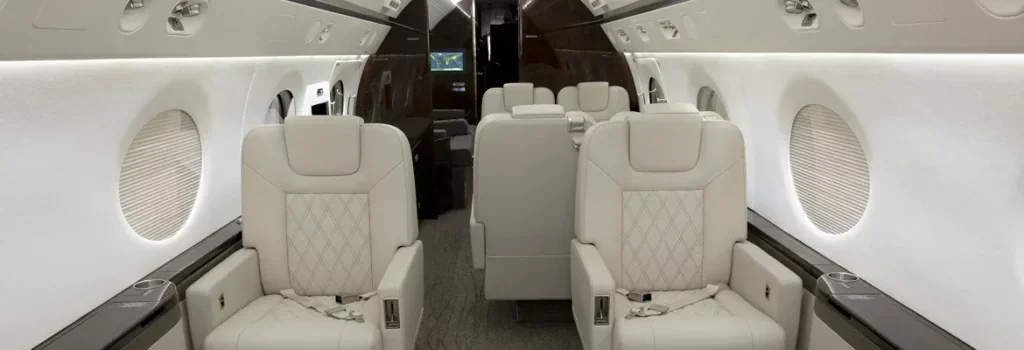
Interior refurbishment and avionics upgrades completed by Duncan Aviation transformed this G550. Their finish shop came up with a creative solution to achieve a “plated” finish on the cabin handrails. They sanded the existing rails down to bare aluminum and applied a transparent Cerakote finish to match the clear-coating on the cabin plating.
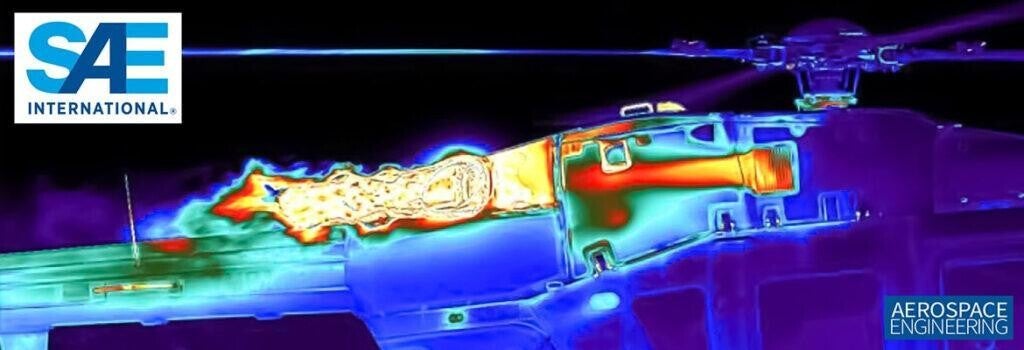
It is recommended that the epoxy seal coat in the current coating system be replaced by Cerakote to alleviate and remove the delamination and burning in the inner skin of the engine cowling when the aircraft is hovering. Moreover, the recommended Cerakote C-7700 Q can be used to paint on current engine cowlings to improve their heat resistance. Cerakote has long been used in automotive industries to provide a thermal barrier for exhaust systems to reduce the engine compartment temperature, the results obtained from this study for the first time suggest its applicability in aircraft.
This article is based on SAE International technical paper, “Improve Heat Resistance of Composite Engine Cowlings Using Ceramic Coating Materials, Experimental Design and Testing,” by Yucheng Liu and Ge He, Mississippi State University, and Thomas Sippel, Airbus Helicopter Inc., doi:10.4271/2017-01-2130.
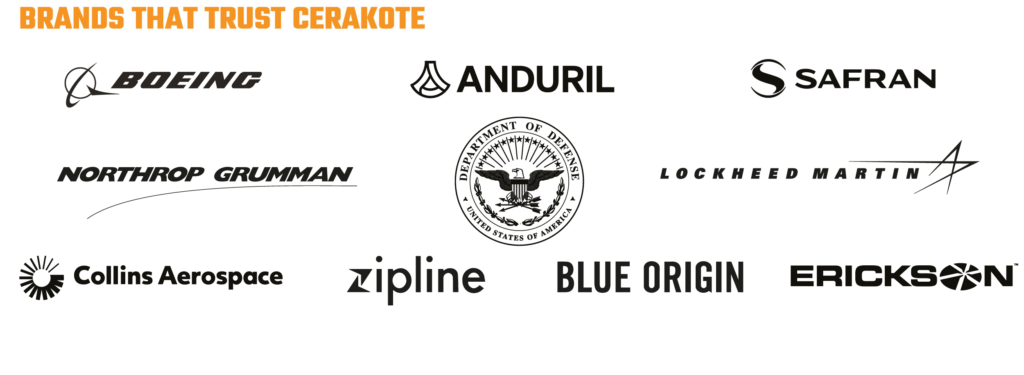